
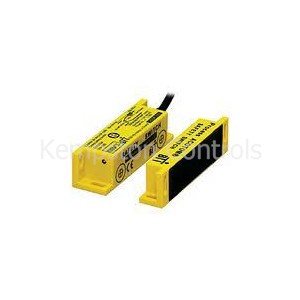
Note that performance level (PL) ratings under EN/ISO 13849-1 are also correlated with probability of dangerous failures per hour (PFH d) values, so direct comparisons can be made between EN/ISO 13849-1 performance levels and EN 62061 safety integrity levels.Get prepared for the challenges of Industry 4.0-with smart solutions from Pepperl+Fuchs. Once the safety integrity level (SIL) has been assigned, the system is broken into subsystems, whose architectures are classified as A, B, C, or D, with D being the “highest,” or safest. Each architecture is associated with a formula to determine the probability of dangerous failure per hour (PFH d) of the subsystem. SIL ratings are determined by a matrix that ranks the severity of injury and the injury classification.

The SIL rating is then chosen from a matrix that plots the severity scores (Se) and classes (Cl). probability of avoiding or limiting the harm (Av)ĮN 62061 assigns a safety integrity level (SIL) from 1 to 3 based on the severity of potential harm and the probability of the harm occurring.Įach of these parameters is scored from 1 to 5, with 5 being the “worst,” or least safe situation, and their scores are summed to determine a class (Cl).frequency and duration of exposure (Fr).

The probability of harm occurring is broken down into three parameters: The severity of potential harm is given a score from 1 to 4, with 4 being the most severe. The EN/IEC 62061 machine safety standard (often written as just EN 62061) assigns a safety integrity level (SIL) to each function based on the severity of the potential harm (Se) and the probability of the harm occurring. Note also the correlation with probability of dangerous failure per hour (PFH d) rates. This chart shows the relationship between Category, Diagnostic Coverage, and Mean Time to Dangerous Failure for PL levels under EN/ISO 13849-1. The architecture category is determined by combining the performance level (PL) with quantitative measures of diagnostic coverage (DC) and mean time to dangerous failure (MTTF d). Once the performance level has been determined, the architecture that facilitates the defined performance level is classified into one of six categories (“B” and 1 thru 5, with B being the least safe and 5 being the most safe). EN/ISO 13849-1 assigns a performance level (PL) rating from a to e, with PLe being the highest risk. The performance level (PL) is designated by an alphabetic character, a thru e, with PLe being the highest risk level. possibility of avoiding the hazard or limiting the harm.frequency and/or exposure time to the hazard.The EN/ISO 13849-1 machine safety standard uses a qualitative risk graph, or flow chart, to assign a performance level (PL), based on three criteria: Although this directive is specific to the European Union (EU), it is recognized and followed in other regions around the world, to better facilitate equipment shipments outside the EU. The EU Machinery Directive requires that machine manufacturers eliminate or minimize hazards as much as reasonable, apply necessary protective measures against hazards that cannot be eliminated, and inform users of the risks that remain and requirements for training or personal protective equipment.
#Bti safety switch max 4 iso#
Although their methods for performing risk assessment are different, both standards - EN ISO 13849-1 and EN 62061 - when correctly applied, achieve the same result. Both standards are harmonized to the EU Machinery Directive 2006/42/EC, which defines the Essential Health and Safety Requirements (EHSR) for machinery. Machine safety is governed by two standards: EN/ISO 13849-1 and EN/IEC 62061.
